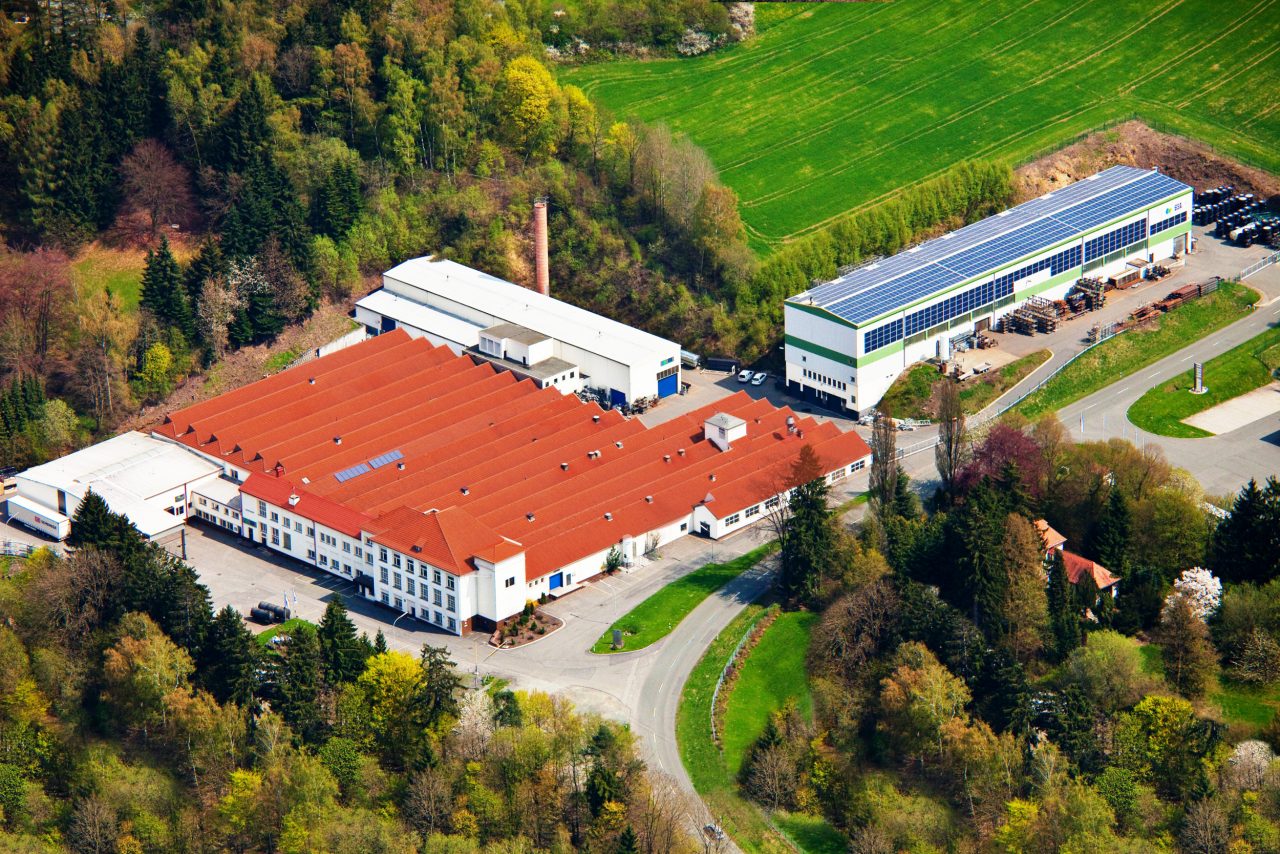
An award-winning family company in the vicinity of Lake Schliersee makes use of FAN technology for separating the sludge.
The Lantenhammer distillery in Bavaria is nearly one hundred years old: In 1928, Josef and Amalie Lantenhammer produced their first gentian schnapps in Hausham, marking the start of a long and passionately pursued family tradition. Almost one hundred years later, Lantenhammer is a modern, cosmopolitan company with a diverse range of brand products from “Gin Chilla” to Bavarian vodka and rum as well as fruity liqueurs featured on drink menus throughout the country and an inviting distillery where visitors can enjoy fascinating tours and tastings. The company philosophy is built around a family atmosphere – the distillers are all trained in-house, making them part of the “family” – and natural products without artificial additives that mature in historic, breathable stoneware vessels for up to three years.
After decades spent on the shores of Lake Schliersee, the Lantenhammer distillery moved back to Hausham in 2014, where it built and later expanded its new plant with visitor centre and shop. This change made it necessary to consider how to dispose of the sludge – the residues from distillation: Before it can be introduced into the public sewer system, coarse solids and fibrous material must be separated out. This job is now handled on a daily basis by a FAN Separator 1.1 300.
The sludge from the distillery consists of fruit pulp (10 per cent water) and yeast. The holding tank has a capacity of 3000 litres, and the material temperature is a hot 75 °C. Another challenge for the separation consists in handling the various different substrates since Lantenhammer produces a variety of fruit schnapps and liqueur types.
Master distiller Benedikt Igler, an enthusiastic practitioner of his craft, explains what happens to the two phases after separation: “The liquid phase goes into the storage tank for cooling and is fed into the sewer at less than 35 °C. The solids are delivered to a composting facility.” Igler is also responsible for maintenance of the separator, which is washed after every use and serviced in the in-house workshop when necessary. This keeps all the work within the successful “Lantenhammer family”.
The installation consists of a FAN PSS 1.1 300 with a 0.75 sieve and no weights
Example: Peach sludge:
Continuous feed via holding tank
DM content of the input material: About 6-8%
pH: 5.5
Throughput: 5-6 m³/h (varies depending on fruit type)
DM content of the solids leaving the machine: 22-24%